Isfahan Minakari
(1).jpg)
The art of Minakari or Enamelling is called miniature of fire as well as the decoration of metal and tile with mina glaze. Minakari or Enamelling is the art of painting, colouring and ornamenting the surface of metals by fusing over it brilliant colours that are decorated in an intricate design.
Mina is the feminine form of Minoo in Persian, meaning heaven. Mina refers to the Azure colour of heaven. The Iranian craftsmen of Sasanied era invented this art and Mongols spreaded it to India and other countries. French tourist, Jean Chardin, who toured Iran during the Safavid rule, made a reference to an enamel work of Isfahan, which comprised a pattern of birds and animals on a floral background in light blue, green, yellow and red.
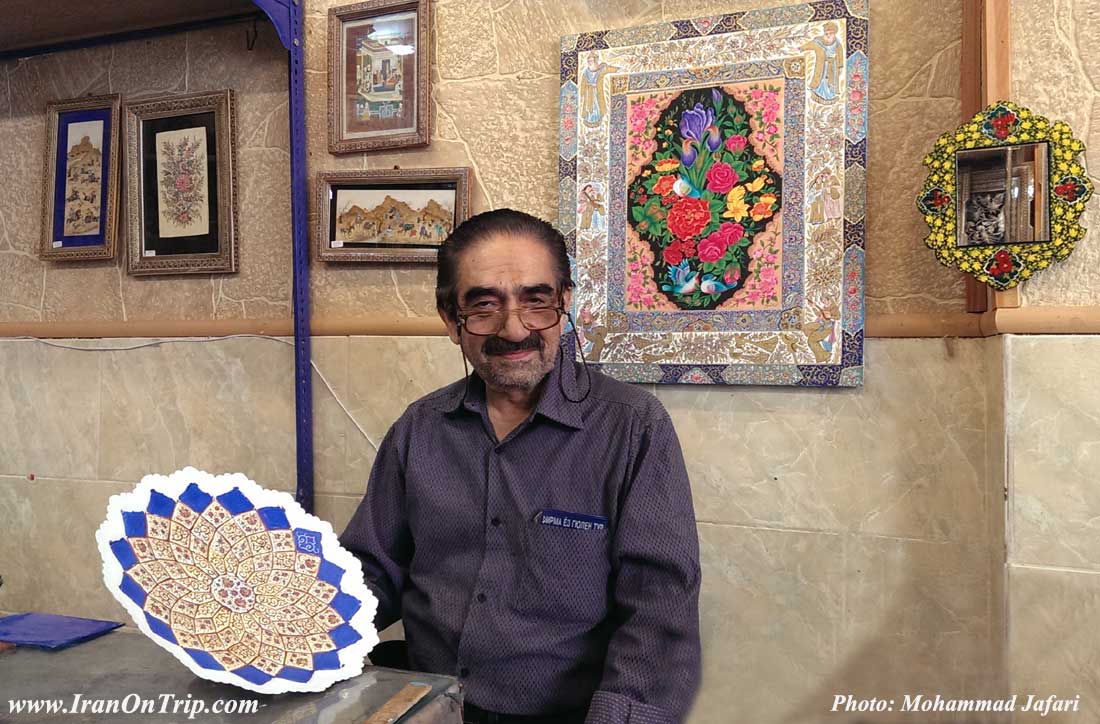
Some experts link the historicity of enameling in Iran to the Arsacides and Sassanid periods. However, the use of this art in the Islamic period is not clear before the reign of the seventh ruler of Mongol empire’s Ilkhanid division in Iran, Ghazan Khan (694-703 AH) who introduced Mongol Persia to Islam.
Ghazan Khan acquired the science of chemistry in a short period and preferred to use his knowledge and endeavors for the art of enameling.
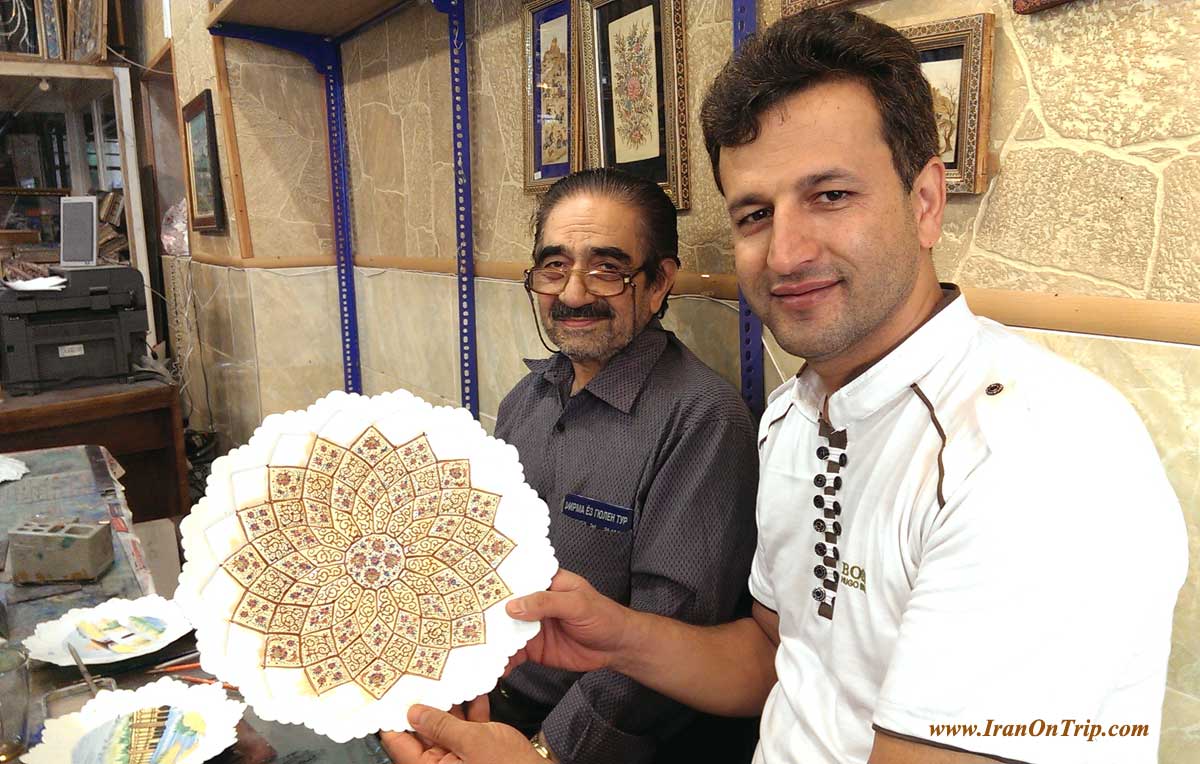
Fine silver is used in almost all enameling because the enamel (glass) melts and sticks best to a pure metal. In simple words, enameling is the process of making metal models (fine silver usually) and then melting various colors and types of glass on to the model to create an objet d’art.
In a more scientific approach, enamel (or vitreous enamel or porcelain enamel in US English) is defined as the colorful result of fusing powdered glass to a substrate by firing, usually between 750 and 850 degrees Celsius.The powder melts, flows and hardens to a smooth, durable vitreous coating on metal, glass or ceramic. According to some sources, the word enamel comes from the High German word smelzan (to smelt) via the Old French esmail. Used as a noun, an enamel work is a usually small decorative object, coated with enamel coating, such as a champlevz or a cloisonnz.
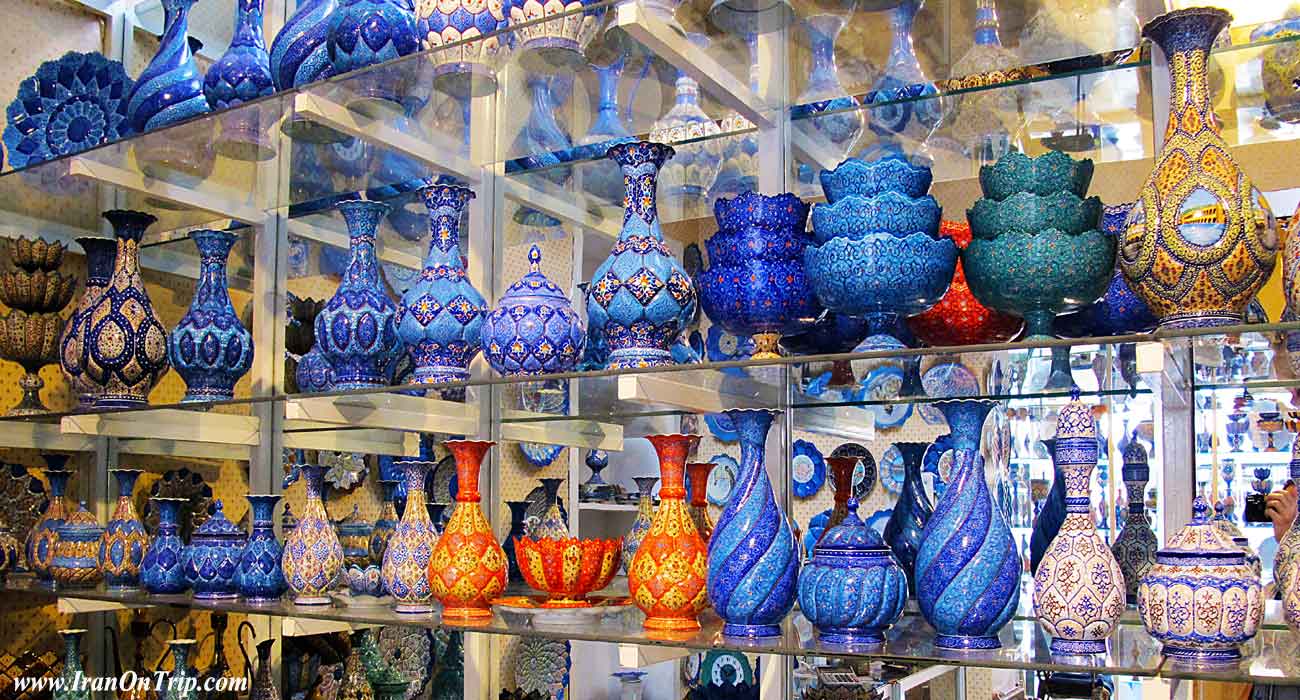
The paintings or patterns used for enamel works in Iran are traditional designs depending on the taste and preferences of the artist. In the Iranian version of enameling, copper and silver are the most dominant metals used. There are also special tools used in this ancient artistic endeavor such as furnace, pliers, press machine, brush and so on.Enamel is usually used to embellish vase, jewelry and candleholder in addition to doors and chandeliers of holy shrines. Isfahan is the most important Iranian enameling hub. Enamel works can be washed with lukewarm water, soap and even ordinary detergents.
Gold has been used traditionally for minakari jewellery as it holds the enamel better, lasts longer and its lustre brings out the colours of the enamels. Silver, a later introduction, is used for artefacts like boxes, bowls, spoons, and art pieces while Copper which is used for handicraft products were introduced only after the Gold Control Act, which compelled the minakars to look for a material other than gold, was enforced around the world.
Enamel working and decorating metals with colorful and baked coats is one of the distinguished courses of art in Isfahan. Mina, is defined as some sort of glasslike colored coat which can be stabilized by heat on different metals particularly copper. Although this course is of abundant use industrially for producing metal and hygienic dishes, it has been paid high attention by painters, goldsmiths and metal engravers since long times ago. In the world, it is categorized into three kinds as below:
1- painting enamel
2- Charkhaneh or chess like enamel
3- Cavity enamel
What of more availability in Isfahan is the painting enamel of which a few have remained in the museums of Iran and abroad indicting that Iranian artists have been interested in this art and used it in their metal works since the Achaemenian and the Sassanid dynasties. The enamels being so delicate, we do not have many of them left from the ancient times. Some documents indicate that throughout the Islamic civilization of and during the Seljuk, Safavid and Zand dynasties there have been outstanding enameled dishes and materials. Most of the enameled dishes related to the past belong to the Qajar dynasty between the years 1810–1890 AD. There have also remained some earrings. Bangles, boxes, water pipe heads, vases, and golden dishes with beautiful paintings in blue and green colors from that time, Afterwards, fifty years of stagnation caused by the World War I and the social revolution followed. However, again the enamel red color, having been prepared, this art was fostered from the quantity and quality points of view through the attempts bestowed by Ostad Shokrollah Sani'e zadeh, the outstanding painter of Isfahan in 1935 and up to then for forty years.
The technique of this art entails perseverance and deliberation. In Minakari an ornament is crafted in silver and then the artist draws the desired design. It is then outlined by the engraver to make the enamel adhere firmly to the metal. Enameller then brushes the ornament on the engraved design with special colors called Mina in red, green, black, yellow, blue etc A single piece of Mina pass through many bands before it reaches completion.
The intricate geometric design pattern of Minakari symbolizes various elements of a belief structure that has been evolved since the dominance of Mithraism era in the Iranian plateu. Here the center medallion symbolizes Mithra, the sun.
Now after a few years of stagnation since 1992, this art has started to continue its briskness having a lot of distinguished artists working in this field. To prepare an enameled dish we should make the following steps:
The process of making Minakari is not very complicated. First, a metallic substrate like copper, silver or brass is chosen and shaped by expert coppersmith. This layer is the base of enamel. In the past, the enamel had been
applied to tile, ceramic or glass, but nowadays copper is more often used because it is malleable and flexible. A new and firsthand copper layer is better than a recycled one.Then, the body is covered with a white glaze using the dipping technique. Next, it is heated at a maximum temperature of 750°C and the body is recoated with a higher quality glaze and heated again.
This function is usually repeated three to four times. Generally, the enamel glaze is made of silicon, magnesium, potassium, lead, precious stones, feldspar, kaolin, zirconium, boric acid and tin.The glazed and heated metal body is now ready for any kind of design, which depends on the creativity of the artist. This step is called painting with magic colors.
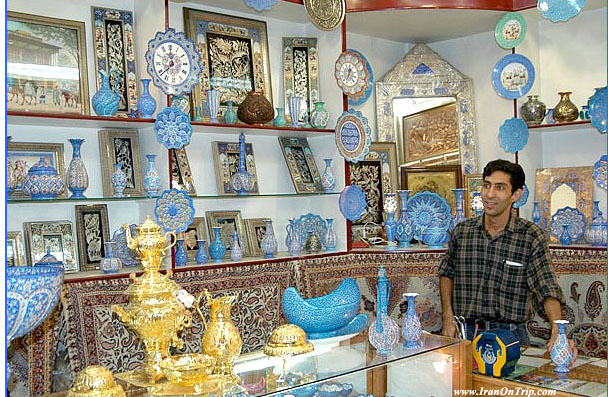
These colors attained from the following chemicals:
1- A white glaze: Tin, lead crystal, flint
2- Turquoise color: Tin, lead crystal, flint, copper shingle
3- Yellow: Iron oxide, tin oxide and lead oxide
4- Black: Iron oxide , manganese dioxide, lead, cobalt oxide
5- Red violet: Crystal, ammonium nitrate and dissolved gold
6- Green: Copper shingle, flint glass (stone), lead chromate
7- Brown: Chromium oxide green, iron oxide, zinc oxide
8- Blue: Cobalt oxide, zinc oxide, flint.
After the painting is complete, the enamel plates are sent back to the furnace, but this time temperature is about 600oC. This brings out the final colors. In the past, inorganic dyes were used in this art, but at present chemical colors are used as well.The criteria, which could affect the quality of enamel, are selection of an appropriate metal, decoration, standard heating and finally, elegance and accuracy of artist.Things that can damage Minakari include damage of the edges of the body caused by mechanical impacts or lack of appropriate heating in furnace, faults in metal base (such as having a streak in the metal layer) or a lack of strong junction between different layers.Different kinds of local symmetrical patterns are used in Minakari paintings, such as ‘eslimi’, which is one of the well-known Islamic patterns also used in traditional architecture, painting with one color as the background and then using bright golden colors on it, using a very fine pen to make miniature patterns and then beautifying the background with green, blue or brown color, or designing on a colorful heated body by using the golden Mina color.The beauty of the work depends on the period of heating and the artist’s precision. The final calligraphy is designed on the body before stabilizing the Mina by heating in the furnace.The biggest risk to the enamel is separation of the decorated surface because of a mechanical impact. Hence, care should be taken while transporting the work. If a part of enamel is separated, it should be repaired immediately otherwise it can cause other parts to separate.The enamel can be washed with a sponge and warm water, and this does not cause any problem, because the enamel is covered with a transparent glaze. Iranians are well known for producing Minakari of the highest beauty.The greatest master of enameling of Isfahan is Shokrollah Sanizadeh, whose ancestor was a renowned painter. One of the invaluable works of this master was used for printing a stamp for commemorating Iranian handicrafts in 2008-9 and registered as national heritage. The original objet d’art is being kept at the Museum of Traditional Arts and Handicrafts.Among the distinguished students of Sanizadeh, one could refer to Gholamhossein Feizollahi, who is dexterous in designing beautiful patterns.There are quite a few artists in Isfahan who produce enamels that are very exquisite. There is great demand for these works, because of its artistic value and relatively low price. These artists present their works in Chahar-Bagh Street and the vicinity of Naqsh-e Jahan Square.
.....
.....
.....